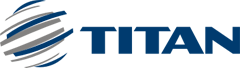
TITAN has been actively investing in the entire value chain of building materials, including aggregates, ready-mix concrete, dry mix mortars, building blocks and fly ash beneficiation products. Vertical integration is a major priority of corporate strategy, as the Group pursues new sources of growth by leveraging the benefits of an expanded presence in existing markets.
In 2011, turnover from areas other than the core cement business represented 27% of total.
TITAN has a strong degree of vertical integration in the Eastern U.S.A. and in Greece and a growing presence in the regions of South Eastern Europe and the Eastern Mediterranean.
An innovative and integrated building materials group
TITAN Group is a leader in the processing and management of fly ash with a decade of experience in the field.
Separation Technologies LLC (ST), acquired by the TITAN Group in 2002, develops commercial applications for a proprietary electrostatic separation process that has applications in a wide range of materials. The ST separator converts fly ash, an industrial waste produced from the burning of coal in power plants, into a sustainable building material used in the construction sector, ProAsh®.
For concrete industry users, ST creates a reliable product that provides cost-savings while increasing the strength and durability of the concrete. At the same time, disposal of fly ash in landfills is avoided, demonstrating that waste recovery can be a sustainable solution which offers business opportunities and benefits to the environment and society.
Separation Technologies offers a range of products for a large number of specific applications.
http://www.stiash.com
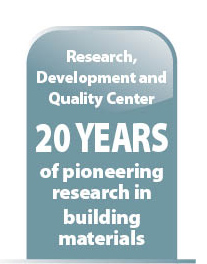
Committed to long term sustainable development
In 2011 TITAN’s Research & Development and Quality Centre entered its 20th year of pioneering research in the building materials field, while seeking ways for the Group to best fulfill its sustainability mission. The Centre technically supports production plants, advising on issues ranging from the assurance of raw materials to quality optimization and control, while researching available opportunities for the production of environmentally friendly cement and other building materials.
The Centre’s current projects include research on the heat consumption characteristics and cost containment opportunities of using alternative fuels and alternative raw materials; development of new products, like pervious concrete and applications for both concrete and mortar to foster sustainability, broadening the firm’s expertise in the life cycle analysis of building materials. These are just a few of the numerous research initiatives currently underway within TITAN Group. TITAN’s Research & Development and Quality Centre is an active member of various collaborative projects with academia, research institutes and industry bodies across Europe.