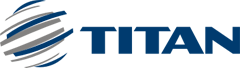
< Greece and Western Europe
Alternative fuels installation (Thessaloniki cement plant, Greece)
At a time when recycling is not just a trend, but a necessity and a solution to one of the major problems facing our planet, the cement industry has a positive contribution to make towards the protection of the environment through the utilization of alternative fuels in the production of cement.
The use of alternative fuels to replace conventional non-renewable fossil fuels, like coal, pet-coke or lignite, is an essential requirement for sustainable development.
Alternative fuels, especially those with high biomass content, can help reduce CO2 emissions footprint.
One of the newest plants in the TITAN Group, the Thessaloniki cement plant has a rotary kiln designed to use alternative fuels at a high substitution rate. In 2011, the installation of a unit that can receive, store and feed alternative fuels was completed. The installation has a silo with a capacity of 340 m3 and can achieve a maximum kiln feeding rate of 10 tons/h.
The installation is designed according to the ATEX European Directive, allowing for operation in a potentially explosive atmosphere. In addition, the unit is equipped with a closed-loop system that guides all exhaust gases coming out from the de-dusting bag filters to the kiln burner, thus avoiding any odor leakage to the environment. The system is suitable for many different types of alternative fuels like rice husk, RDF/ SRF and any other alternative/biomass type solid fuel. The new installation can serve as a solution to the issue of waste management faced by the local municipalities especially that of dried sewage sludge. Such material can be handled safely and in an environmentally friendly way, with multiple benefits for the local community, the plant and the environment.
The total cost of the investment was €2.8 million.