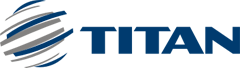
< Greece
New generation kiln burners (Kamari cement plant, Greece)
As part of the Group’s collective efforts to maximize the use of alternative fuels, along with reducing the NOx emissions, a project for replacing the old burners of both rotary kilns was carried out. The total investment cost was about €0.4 million. The new burner systems designed by Unitherm Cemcon are tailor-made to meet the specific requirements of TITAN’s kilns. Each one of them can feed simultaneously four different fuel types, one conventional fossil type fuel and three alternative fossil/biomass type fuels. In addition, NOx emissions can be reduced using the inherent ability for easy and effective shaping of the flame. The two most important factors for adjusting the flame shape are the deflection angle of the air nozzles as well as the quantity of the air. The design of the injection system allows for rapid and uniform mixing of fuel and air, creating excellent conditions for the combustion of even the hardest burnable fuel. As a consequence, NOx emissions are lower, owing to the reduced quantity of air needed for combustion. This has the additional advantage of reducing the consumption of the abatement agent (urea) used by the existing SNCR system.